Welcome to Hambini Engineering
Latest YouTube Video
In the latest video on the Hambini YouTube Channel, a guy from Paris delivered his S-works Venge for a bottom bracket.
This is quite a common problem it occurs when the epoxy holding the bottom bracket in starts to go brittle and eventually the cup starts to spin.
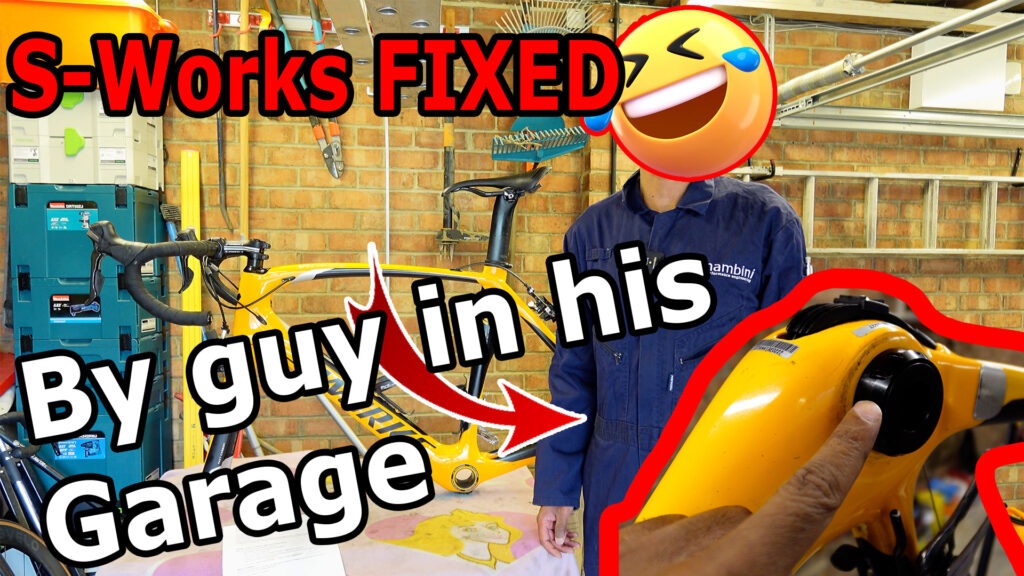
Popular Products
A selection of popular products from the Hambini Webshop. You will find a selection of bearings, tools and bottom brackets. If there is something you cannot find or have a query with. Please use the contact page.
Latest Posts
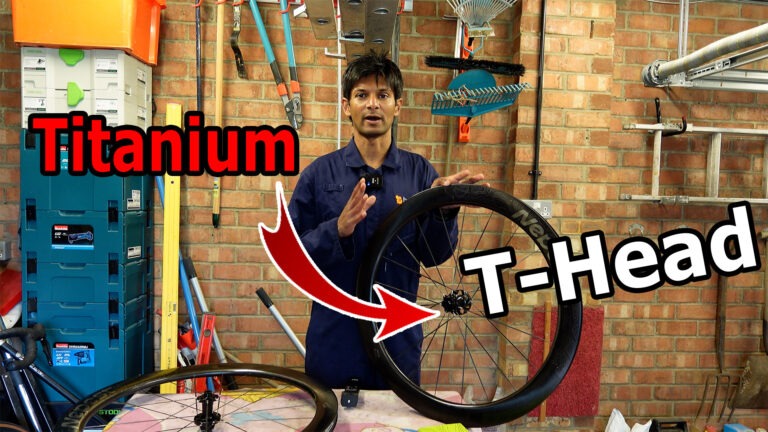
Nepest Nova Carbon Wheelset Review: A shift from Aero towards Mechanical
As the cycling landscape continues to evolve, riders are increasingly demanding more than just low drag figures and flashy decals. They want real engineering, reliability, and performance that holds up under load and over distance. The Nepest Nova carbon wheelset, manufactured in Xiamen, China, enters this space with a strong showing. It combines contemporary design…
![Hambini Bicycle Supplier Discount Codes [100% VERIFIED] - June 2025 2 9 Velo, ICAN, Winspace, Farsports, 9Velo, Elitewheels Discount codes, 100% Verified](https://www.hambini.com/wp-content/uploads/2024/01/discounts-1-768x432.png)
Hambini Bicycle Supplier Discount Codes [100% VERIFIED] – June 2025
The following are discount codes for use with companies with whom I have dealt with and products of good quality. I do not list discount codes for items that are (in my opinion) no good.
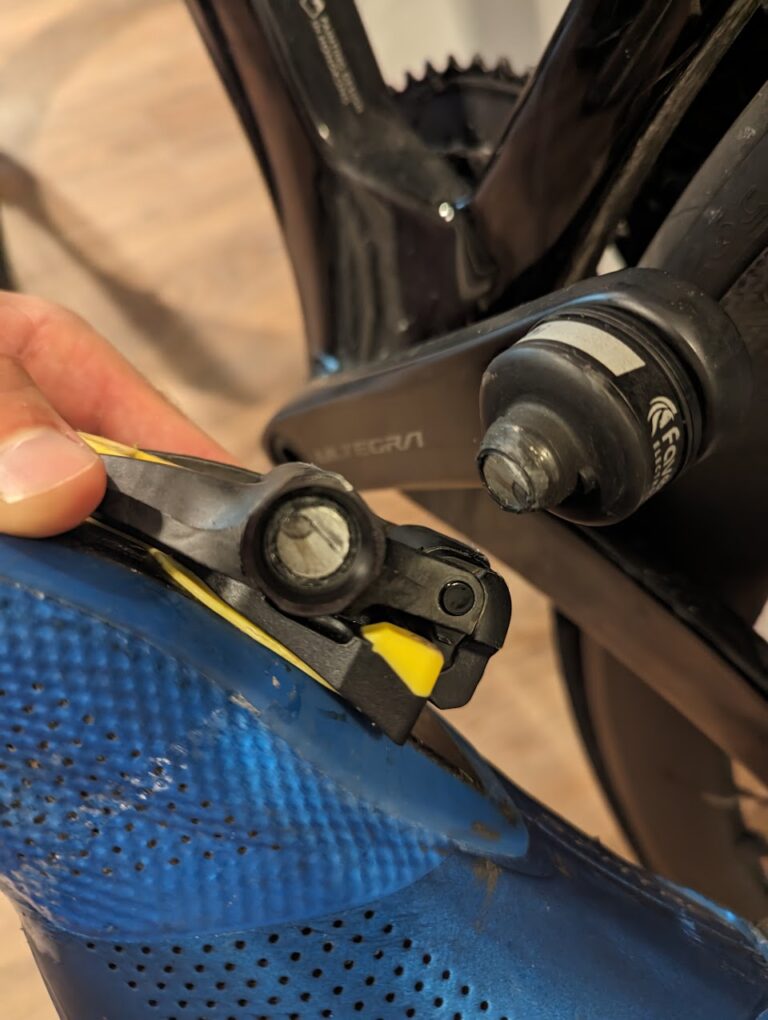
Favero Assioma Pedals: A deep dive into Dysfunction
So, I recently had the pleasure of dissecting the engineering marvel that is the Favero Assioma power meter pedal. And by “pleasure,” I mean I aged about five years in disbelief. Despite the proudly flaunted “Made in Italy” label, these pedals are basically a how-to guide for what not to do when designing cycling equipment….
Popular Posts
![Hambini Bicycle Supplier Discount Codes [100% VERIFIED] - June 2025 4 9 Velo, ICAN, Winspace, Farsports, 9Velo, Elitewheels Discount codes, 100% Verified](https://www.hambini.com/wp-content/uploads/2024/01/discounts-1-768x432.png)
Hambini Bicycle Supplier Discount Codes [100% VERIFIED] – June 2025
The following are discount codes for use with companies with whom I have dealt with and products of good quality. I do not list discount codes for items that are (in my opinion) no good.
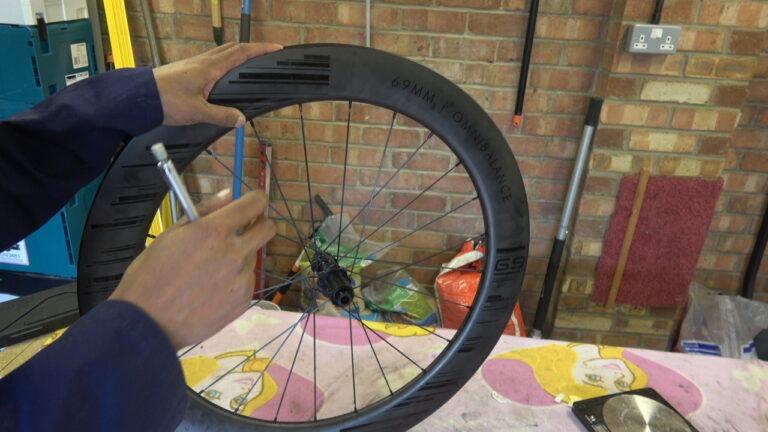
Bicycle Wheel Power Data 50km/h Disc
This post provided aerodynamic performance data for wheels using disc brakes.
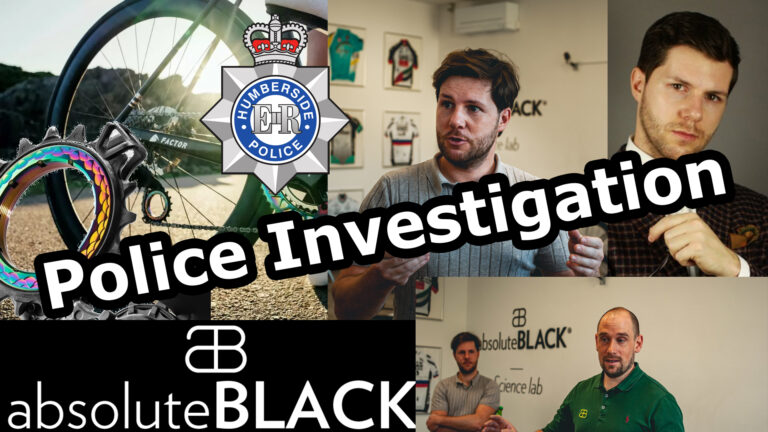
AbsoluteBLACK under Police Investigation
The CEO and Sales Director of AbsoluteBlack are under investigation by UK Police authorities for harassment, intimidation and stalking.
AbsoluteBlack have a history of attempting to suppress negative publicity about their products.
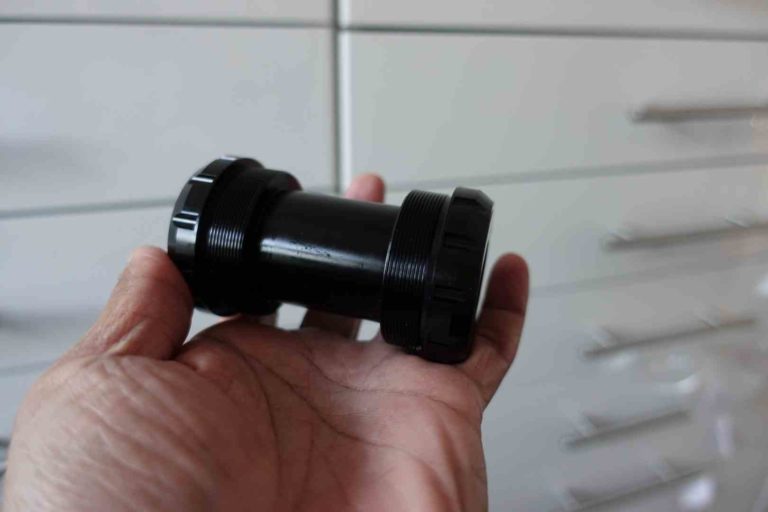
T47 Bottom Bracket: Engineering Guide (Threadfit)
T47 is examined in engineering detail. Some of the quirks associated with the standard, the weights and the frame geometry limitations are discussed. Trek, Felt and Factor variations of T47 dimensional standars are covered.
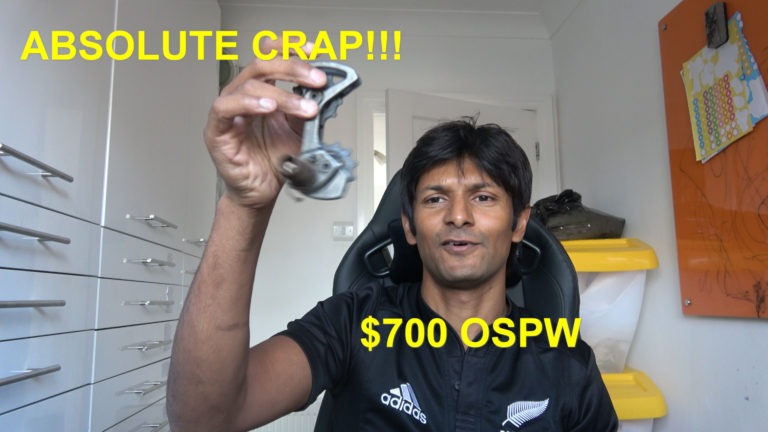
AbsoluteBLACK Hollowcage $700 OSPW leaves company reputation in tatters
AbsoluteBLACK (real name LUCID IP SLU registered in Andorra) were destroyed on social media after their claims about ceramic bearings, power savings and watts were questioned. They systematically curated both their own social media accounts and comments on other accounts. They removed large numbers of comments that questioned their aerodynamic and power claims
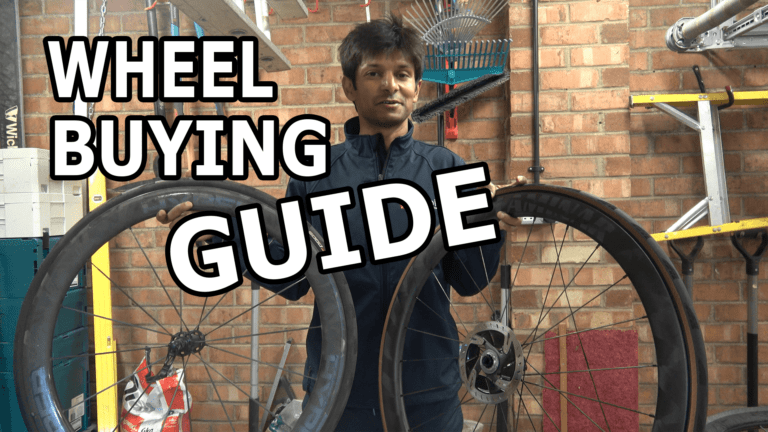
Engineering Bicycle Wheel Buyer’s Guide
This buyer’s guide will allow you to make an informed choice about purchasing a set of new racing bicycle wheels. It covers the main points to consider when purchasing from a technical perspective.