SRAM GXP Cranksets: An Engineering Guide
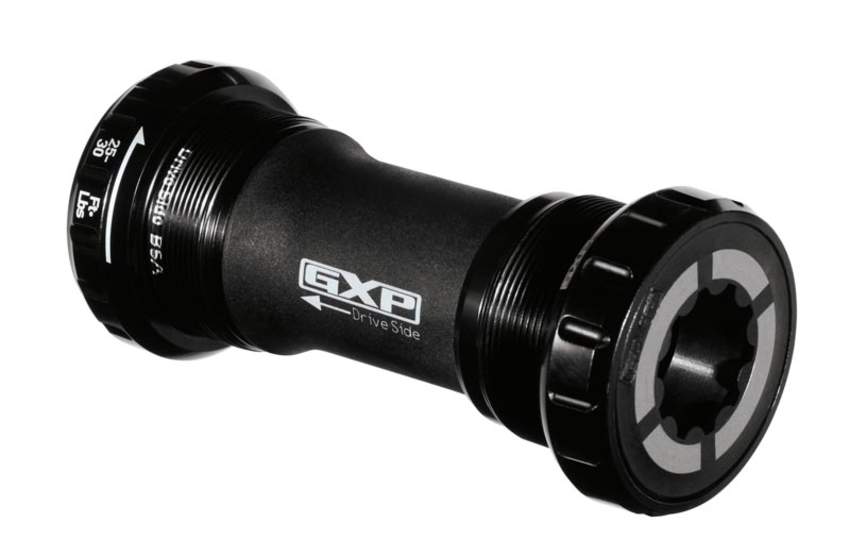
This article will cover the technical and engineering aspects of SRAM GXP. Sram GXP is a very popular crankset standard used by SRAM. It offers an industrial based bearing arrangement and was touted as having the lowest weight and rolling resistance of any crankset bottom bracket standard. The engineering will be analysed in detail. Currently the standard has been superceded in the retail market, but a large base of existing users and OEM customers such as TREK continue to use GXP.
This guide will explain some of the quirks with the GXP standard and why fitting it can be problematic.
History
SRAM GXP was originally a design from the company Truvativ. GXP standing for Giga X Pipe. SRAM bought Truvativ in the early 2000’s and since then it was used as a drop in rival to the advancing Shimano Hollowtech 2 standard. At the time, threaded bottom brackets were common place and both the Shimano and the SRAM standard moved the bearings outwards beyond the extremities of the frame thus increasing stiffness and reducing the amount of cantilevered torque transfer.
From an engineering perspective it is obvious that GXP was designed to skirt around Shimano patents related to Hollowtech 2 whilst maintaining close compatibility to frames. It appears to have been designed so a modification (additional spacer) to a Shimano bottom bracket could be made to allow it to make it GXP compatible.
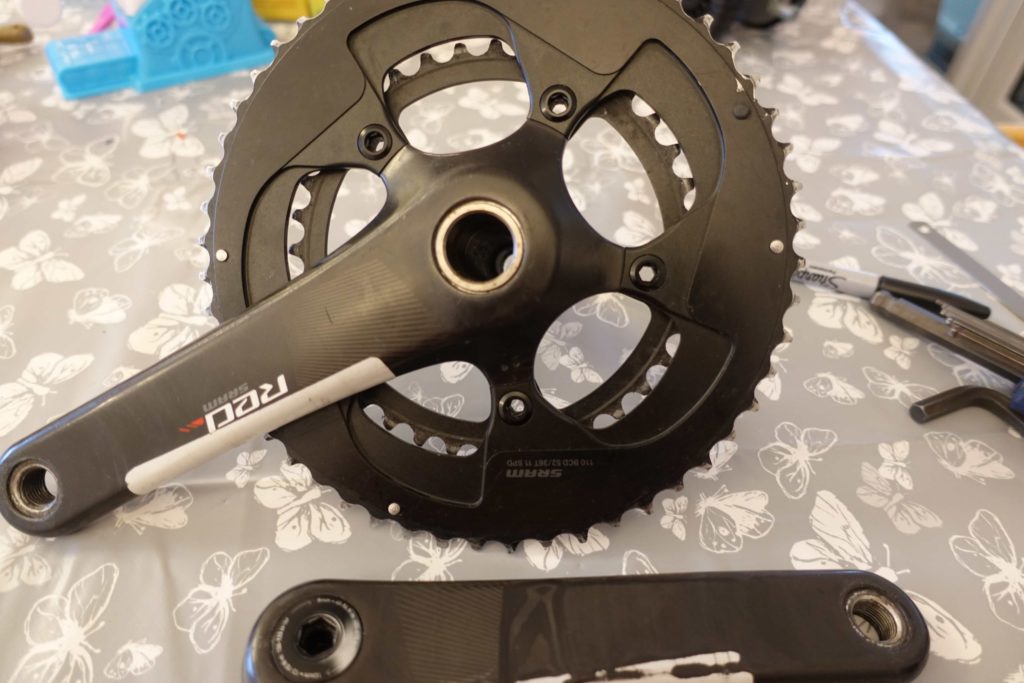
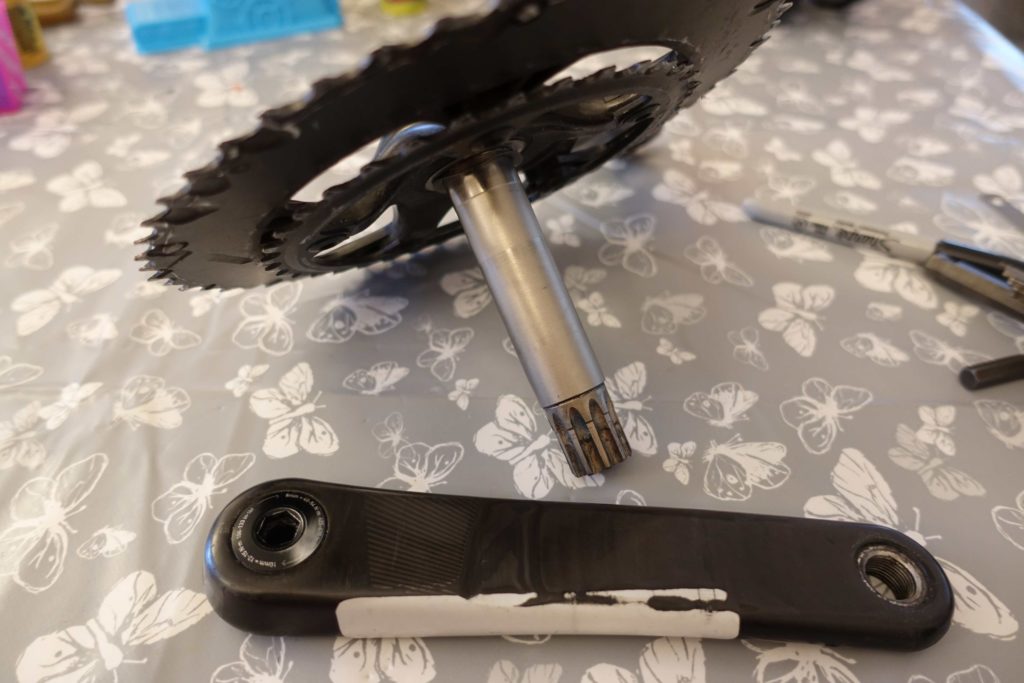
Technical Details
- GXP axles are steel
- The section towards the drive end is 24mm
- The section towards the non drive crank arm is 22mm (stepped)
- The crankset split is on the non drive side and uses a tapered fit (this is problematic, see further on)
- The non drive side crank arm attaches to the axle using a very shallow taper.
GXP was one of the few crank standards that used a stepped shaft and subsequently a fixed/floating bearing arrangement. The other notable exception was Praxis with their M30 standard, this came after GXP and shared many common technical traits albeit in a larger diameter (30mm and 28mm step).
Practical problems
Asymmetrical bearing loading
The action of pedaling causes two forces to be generated. The forward rotation is the most obvious and easily accounted for, this is called a radial bearing load. A less well known force is an axial force which is caused by the Q factor of the pedal force. This axial force places a load on the bearings that tries to push the axle out of the bike frame.
On most cranksets (Shimano, SRAM DUB, 30mm, Campagnolo), the load is distributed to both bearings within the bottom bracket. In the case of SRAM GXP the axial forces are taken up solely by the bearing on the non drive side.
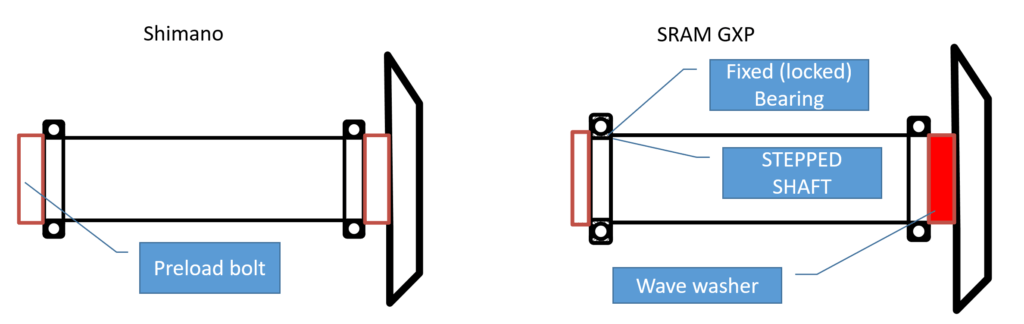
This causes problems as this bearing is heavily loaded and comparatively small in comparison to the potential loads that could go through it. Users often report the non drive side bearing fails quickly and this is the reason for this phenomenon.
The fixed-floating bearing setup that GXP uses is common in the industrial world, many axial fans, pumps and compressors use this setup but those systems are running with constant torque. Pedaling is a notoriously peaky torque application with the majority of torque occurring between 1 and 5 o’clock of the pedal rotation per side.
Many bicycle teams that ran GXP often used to remove the inner clamp ring and emulate a Shimano setup with two floating bearings that were preloaded. From a maintenance, longevity and frictional perspective, this was advantageous.
Poor manufacturing Tolerances
A lot of people are totally unaware of the poor manufacturing tolerances associated with SRAM products. GXP is no exception. There is an issue around the taper of the non drive side. The taper locks the non drive side bearing up. The poor tolerances associated with GXP mean that the length of the 22mm section can vary significantly despite the same bolt torque being applied.
SRAM are obviously aware of this, their solution involves some frankly ropey method of regreasing the bolt and “trying” a few times to induce some surface wear until it clamps up. This is clearly stated in their installation instructions, which can be downloaded below. The appropriate paragraph has been extracted and pasted for convenience.
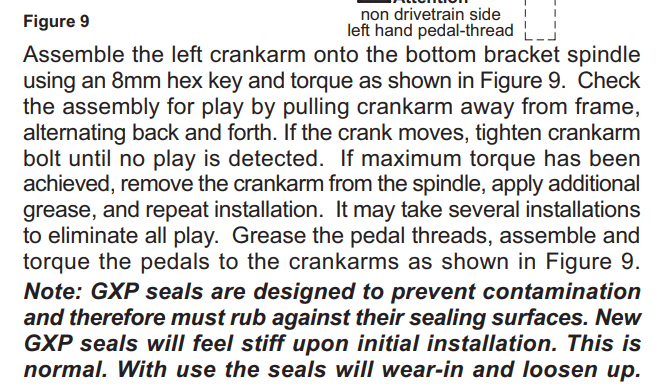
The nominal length of the 22mm section is 12mm but ranges from 10.5 up to 14.5mm, this range is excessive and indicative of a poorly thought-out system or insufficient manufacturing accuracy to ensure repeatability.
The photographs below show how to determine the Distance Between Crank Arms (A) and the length of the 22mm section (B). Both dimensions are required for accurate setup of GXP.
The procedure to work out the A and B dimensions are as follows
- Bolt the non drive side Crank arm on to the axle.
- Mark the point where the axle enters into the crank arm
- Remove the axle and measure from the drive side to the edge of the mark. In this case the DBCA (A) is 93mm, the length of the 22mm Section (B) is 11mm. The length of the 24mm section is by calculation 82mm (93 – 11 = 82).
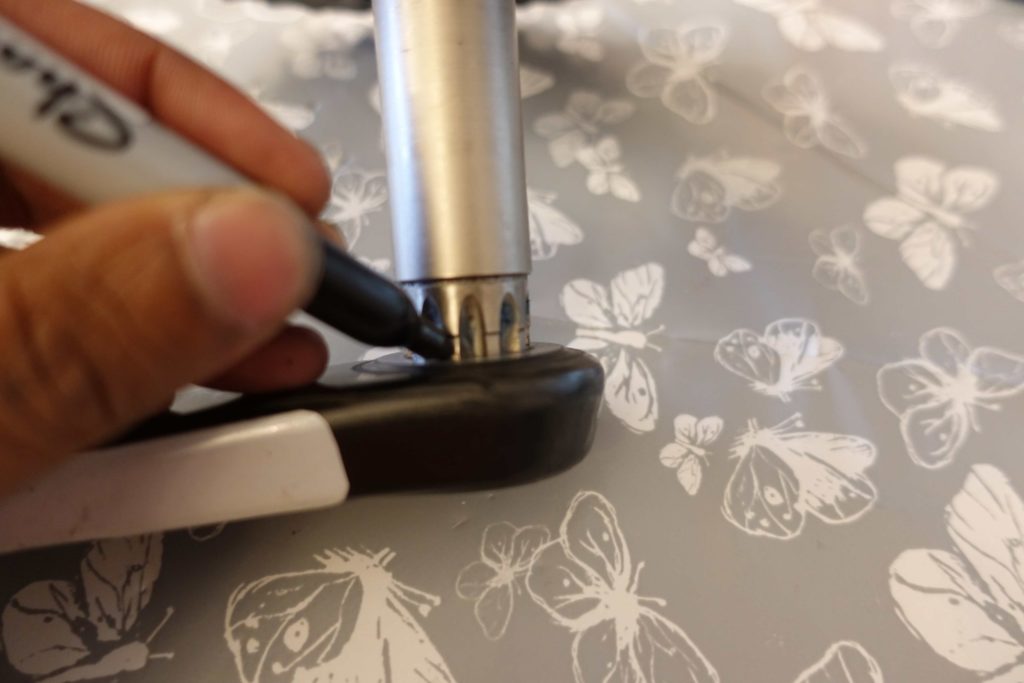
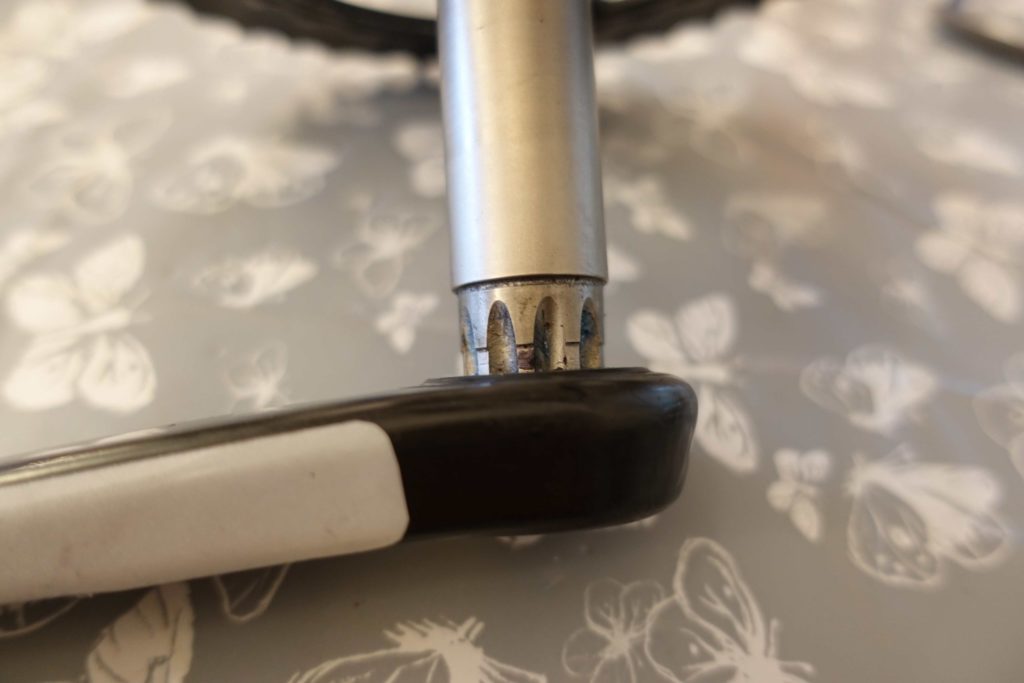
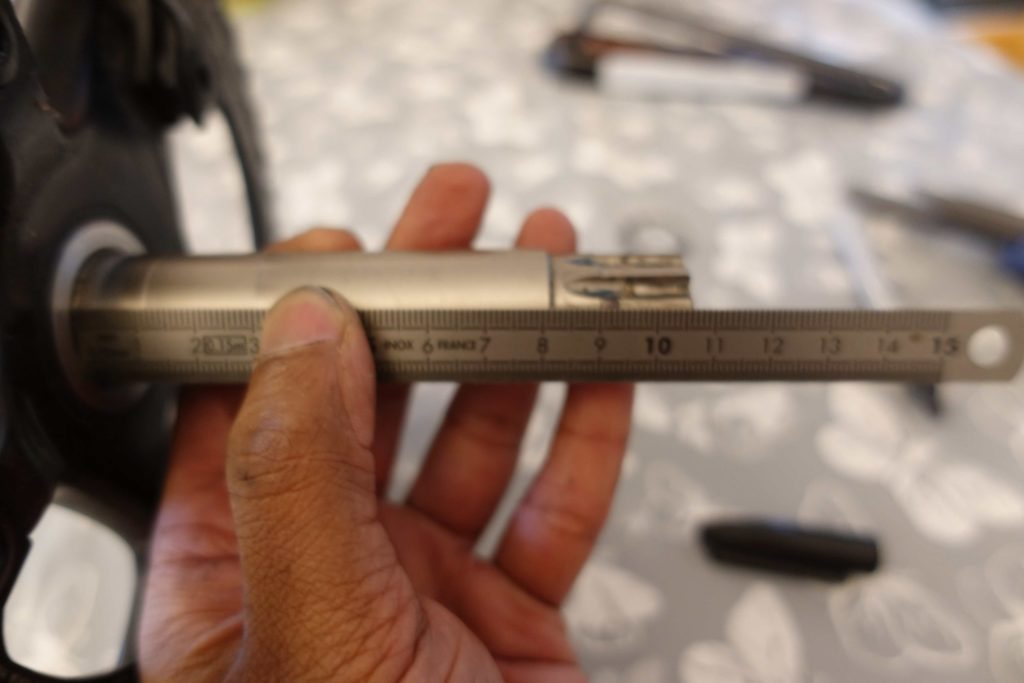
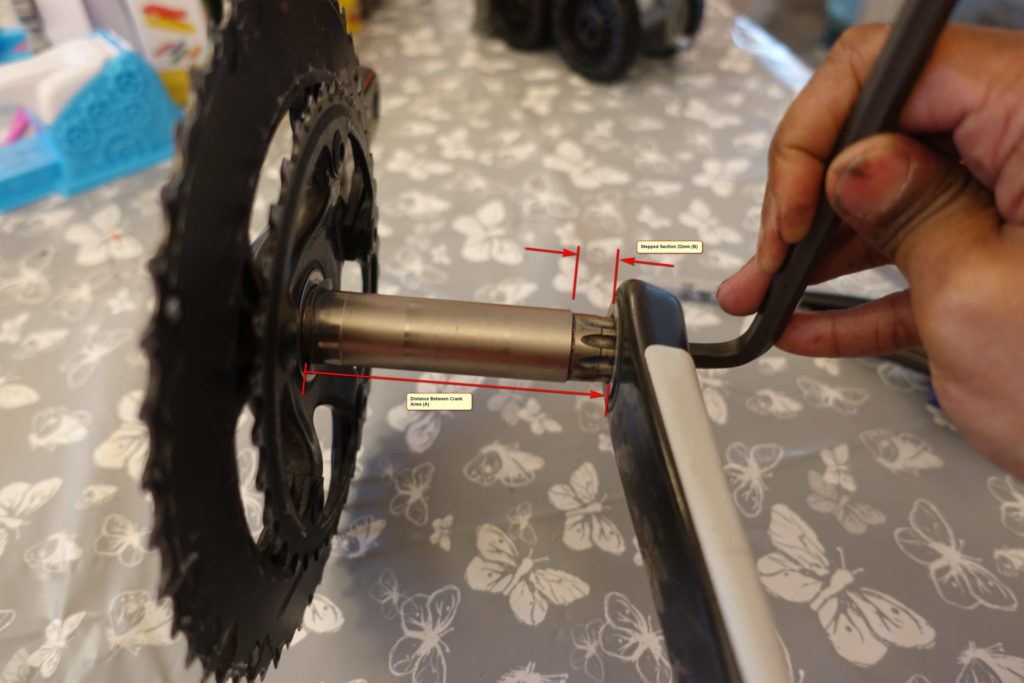
SRAM’s non drive side bearing for GXP has equally poor engineering. The bearing has a 22.2mm (approximately 7/8″), this is to interface onto an axle of only 22mm. The resulting 0.2mm clearance fit is frankly inexcusable.
Hambini GXP Bottom Brackets
it is impossible to create a bottom bracket to work with an axial range of 4mm. Hambini bottom brackets are made with a clamp axial spacing of 12mm, if there is any play after the adequate amount of torque has been applied to the non drive side crank arm. The remainder should be taken up by the addition of additional spacers.
The clamping section on Hambini bottom brackets are 22mm with a H7 fit onto the axle. Hambini GXP Bottom Brackets are available in BB86 GXP and BB30 GXP as off the shelf units. Other frame fits can be made to order
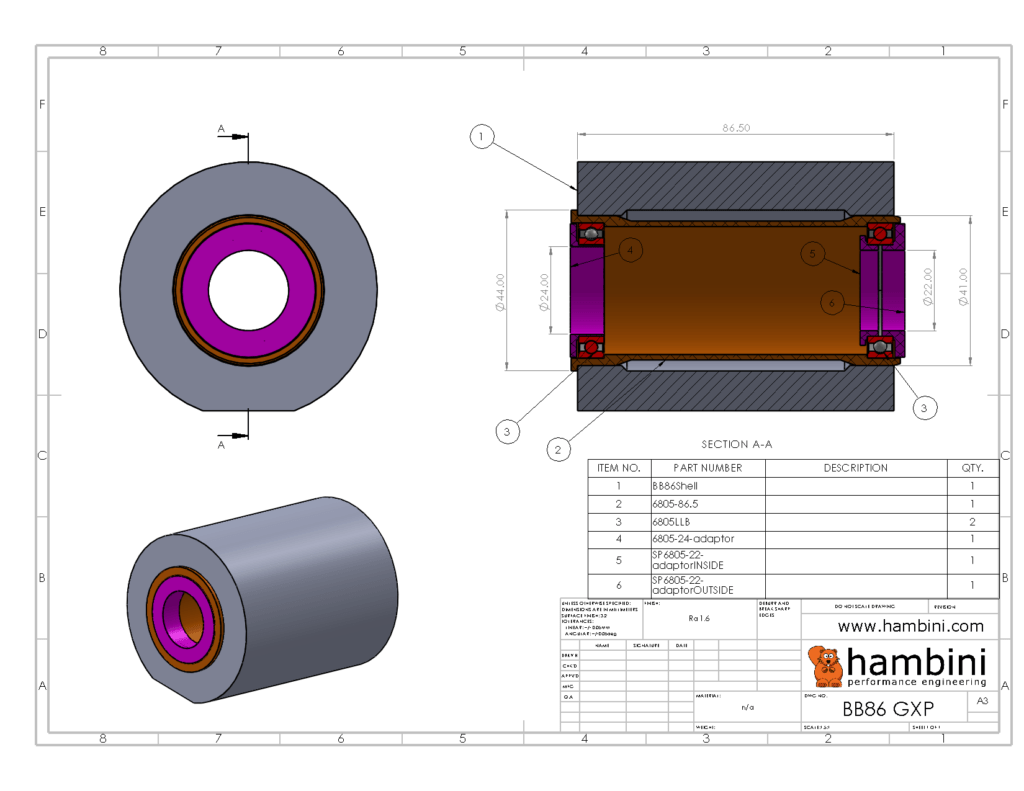
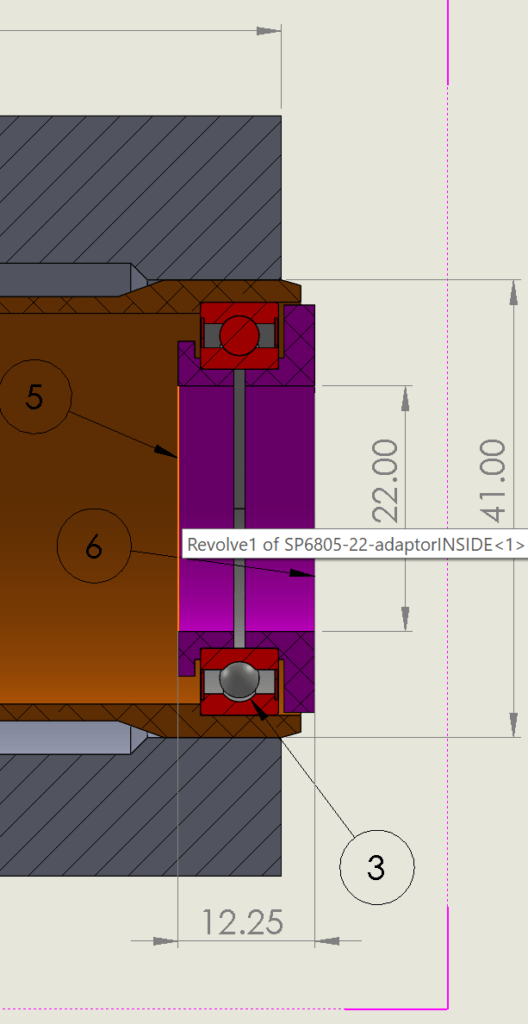
great tutorial. i took a very slightly different approach to achieve essentially the same objective. i measured the face to face distance on the BB (trek madone slr bb90) and used a machined 22mm to 24mm sleeve to fit over the GXP taper and allowed a 1mm tolerance to be taken up by 24mm ID micro shims. The non-drive crank arm essentially nestles up tight against the sleeve but the entire spindle and sleeve are free between the bearings with precise fit being taken up by the micro shims. i was even able to ditch the stupid wave washer. spins great and most importantly, NO BASTARD CREAKING!
No good without pictures!
Hi all,
i have the same configuration. BB86 Pressfit thread with 24mm bearings drive and 24mm with adapter to 22mm. My question is, is it better to use shims on the drive side or the wave washer? When i tighten the crank there is no play at all but when i try to stick a 1mm plastic wedge between the wave washer and the sleeve it works…so some space.
After watching your video Habini i bought a skf 6805 bearing and did some 3d shim development. Next step will be 3d printing the adapters in pla and give them a try in the bike. If it fails i will use another filament like pc or pteg or nylon.
Thanks in advaced und Dankschön
Hi! What is the total weight including bearings and sleeve inserts?
Total weight of the bottom bracket? about 120g but it will vary on the frame type.
I can’t quite picture what you mean by this claim “Many bicycle teams that ran GXP often used to remove the inner clamp ring and emulate a Shimano setup with two floating bearings that were preloaded. From a maintenance, longevity and frictional perspective, this was advantageous.” I have a GXP bottom bracket and crankset with nothing resembling an inner clamp ring. Is there an illustration or more detailed description of this emulated Shimano setup somewhere?
I have the same question. Came here because of many of the problems that the gentleman has described though.
I’m experiencing the same problems with my Praxis M30 crankset. Non-drive side bearing fails magnitudes faster than the drive side. Not quite sure if Enduro bearings makes it better or worse. As it stands, I’m having to replace the non-drive side bearing every season.
Moreover, my first Praxis crankset wouldn’t seat properly on the non-drive side bearing; the bearing was spinning at a different rate than the crank axle. Second Praxis crankset did not have that problem. Not sure if that’s a meaningful observation in regards to tolerance.
I have a 2009 Cervelo R3 SL I am tweaking for my fit and it has BSA threaded GXP BB. Do the threaded BBs have the same failure tendencies? Does the Great Hambini make a threaded GXP BB or a work around for my application?
for threaded, you may as well use the sram oem type.
Can you clarify why threaded BBs can’t be improved on? Also, the axial loading problem can be helped with angular bearings, right?
22.2 ain’t approx 3/4″ – it’s 7/8″ 🙂
I _REALLY_ regret building my bike with this BB and wish I’d known that 1500 miles from the BB was good going.
This is my first SRAM groupset – bought because I fancied a change from Shimano when I built the bike.
I’ll never use SRAM again after this has worn out.
Sir, can you please provide further information on how to replicate this setup?
“Many bicycle teams that ran GXP often used to remove the inner clamp ring and emulate a Shimano setup with two floating bearings that were preloaded. From a maintenance, longevity and frictional perspective, this was advantageous.”
have a read of this https://www.hambini.com/support/installation/hambini-bottom-bracket-installation/#SRAM_GXP_Systems_Prior_to_2020
Does this GxP crankset cause any wear and tear on carbon frames that you know of? Or would any potential issues be limited to the bearings and bottom bracket?
It shouldn’t do. The wear is generally on the bearings.
Just wondering if you have ever seen a 140mm crankset for the Sram gxp bottom bracket. My wife is short yet her 44cm Trek Madonne 3.1 came with a 170 mm crankset. I cannot seem to find a replacement crankset with a much more appropriate 140 mm crank length. Ant suggestions?
I’m afraid not, the only thing I have seen is where an individual used some GXP cranks and redrilled them for his son.
I have two bikes with GXP BB86 bottom brackets running 11-speed Force CX1 cranks and both have been challenging—to say the least—to set up w/o pre-loading the NDS bearing too much…which causes cranks that are very hard to spin. There’s like some magic combination of dust seals + wavy washer + thin washer, but sometimes not a thin washer, and sometimes not a wavy washer and just dust seals. It’s maddening.
Hi Habini
I have Force AXS groupset I was going to install on the Winspace T1500. What would be the compatible BB to use if can’t use the DUB?? Are you saying Sram Force won’t work??
Cheers
Dave
I wouldn’t recommend fitting it in a BB86 shell which is what the Winspace T1500 uses. The bearings end up being quite small. You might be okay or you might not be. It depends on how much power(or torque) you are putting down.
Had to change my BB because the DS bearing was running very rough. After noticing the loose fit of the NDS bearing and measuring the dimensions i couldn’t believe this was a common issue with those cranks. What a f**ked up design…
Had to go with a quick+dirty approach:
i shimmend the NDS bearing on its inner ring with a strip of 0.1mm precision band (length ~68mm, width ground to 11.5mm) to reduce radial play. make sure to put a shallow chamfer on the ends of the strip. This leads to a very snug sliding fit. To secure the bearing axially i used a stack of shims 22x30x0.1mm (in my case 0.4mm in total).
I eliminated the wave washer and used a 2mm thick O-ring instead. The wave washer would have had to be compressed by nearly 1mm on my cranks which puts quite some axial preload on the bearings considering the spring rate of the washer (make sure to check this).
Crank runs very smooth now without any noticable play.
Not a very neat solution but the end justifies the means i guess…