Engineering Analysis: Grease or Retaining Compound
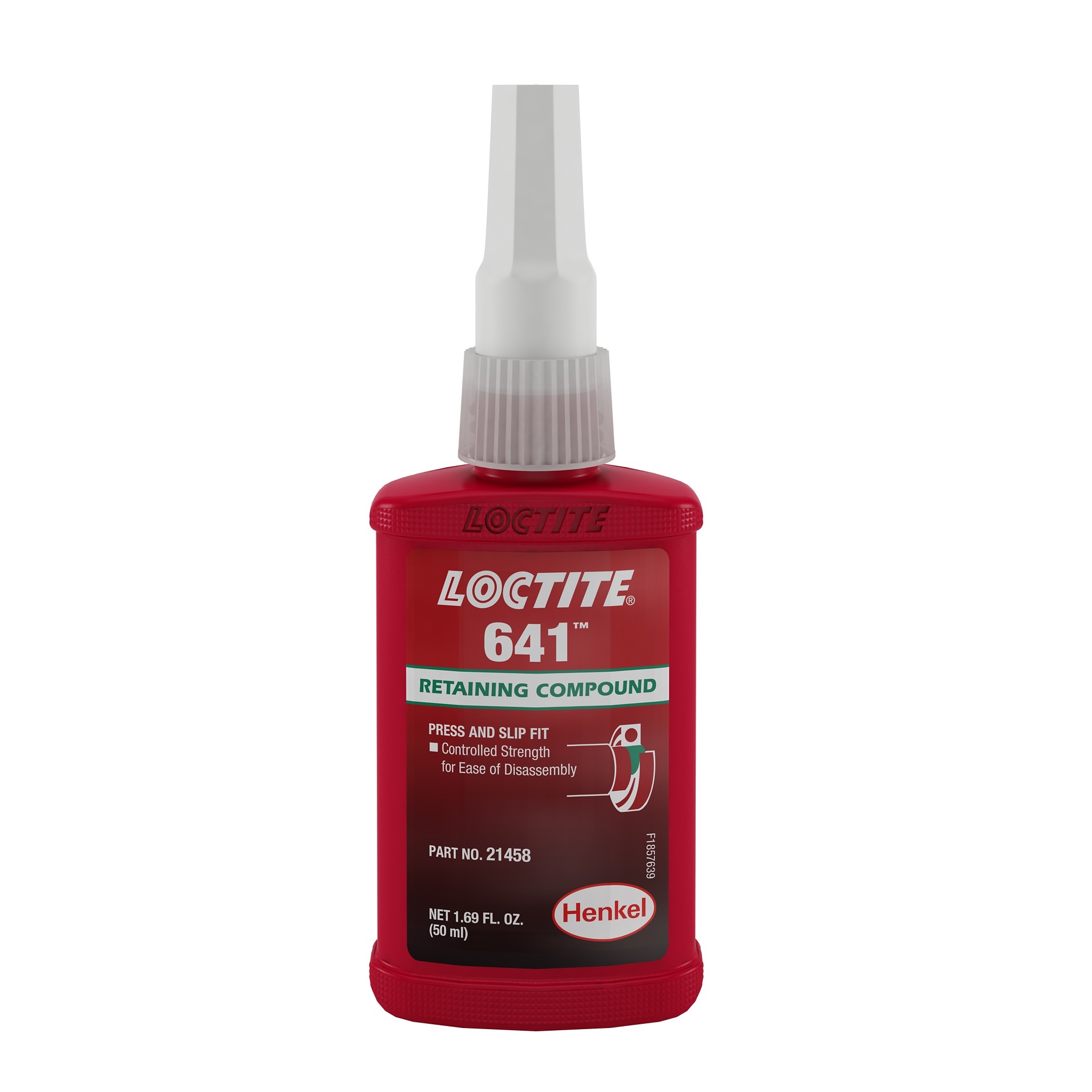
Introduction
Littered in the comments section of almost every Hambini video is a comment about using grease, not using grease or the use of retaining compound. There is lots of misinformation on the internet that has been distributed by the mainstream bicycle media, Forums and others. This post will cover the merits of grease and retaining compound from an engineering perspective.
What is Retaining Compound?
Retaining compound is often generically called “Loctite”, especially in Cycling Circles. This is an incorrect term as the parent company is Henkel and Loctite is the brand and has many different types of retaining compound.
Retaining Compound is essentially a type of anaerobic engineering adhesive that is designed to take up imperfections between cylindrical fitted components. This is why it is called “bearing retainer” in engineering. The exact chemical method of activation will not be covered here. In practice, a small film is applied between the components, the absence of air initiates the action and some 72h later (more on this further down), a bond is created between the cylindrical fits. It is extremely useful where a system assembly needs to be disassembled at some point in the future as the mating surfaces suffer minimal abrasion from installation and removal.
Retaining Compound is available from multiple manufacturers and has different properties. The most common brand is Loctite and the two widely used variants are Loctite 641 and 638.
Loctite 641
Loctite 641 is a medium strength retaining compound. This is by far the most widely used type of retaining compound throughout both cycling and the wider engineering industry. This achieves near full strength within 72h (activator is often required for this speed of cure). It is suitable for metal surfaces and works with plated surfaces and carbon fiber with the use of activator. The manufacturer recommends a maximum gap of 0.1mm for use with this product.
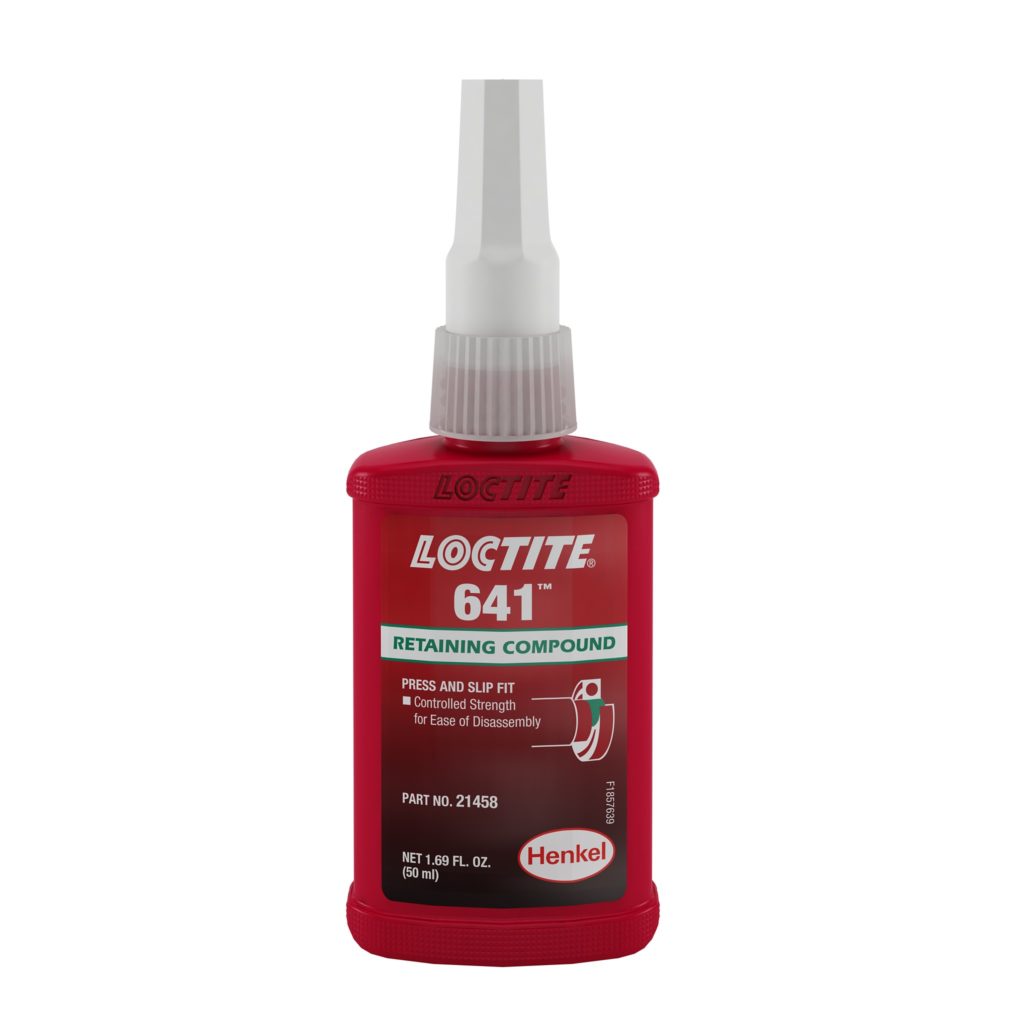
Loctite 638
Loctite 638 is a high strength retaining compound. This has similar properties to Loctite 641 with the exception being it’s ability to work effectively in much larger gaps. The manufacturer recommends a maximum gap of 0.25mm for this product. In practice, carbon fibre and plated surfaces require activator to attain sufficient bond strength.
What is Grease?
Grease is a viscous petroleum mix that is designed to lubricate moving parts or aid assembly. It comes in different grades and chemical compositions and it has been covered in detail the the: Bearing Grease a Practical Guide post.
For general applications, an NGLI 2 grease is used.
The Mechanics of Installation
Instances where the debate between retaining compound, dry fit and grease come up usually involve fits of some description. In engineering terms, a press fit is an interference fit where by mating surfaces of components have sizes such that a mechanical force is required to press one item into the other.
In a perfect interference fit both components are concentric circles. The mating process causes one component to be in compression (the male component) and the other to be in tension (the female component). The radial stresses are sufficient to overcome the maximum axial force and the component stays fixed. The fit is perfect so there is an even distribution of radial forces across the componentry
In real world applications there is some level of radial or axial irregularity which means there is non uniform distribution of stress between the parts. In these scenarios, Retaining compound “takes up the slack” and produces a stronger retention force.
One of the biggest draws in recent years has been a drive towards sustainability and reducing overall life cycle costs. The tribology industry has responded and the fit tolerance required has been consistently reducing over the years.
Modern Engineering Methodology – the case for J fit
For many years, bearing manufacturers recommended housing or shaft fits in the range of m7 or M7. In recent times they have moved towards having a J or JS fit (depending on load). This is on the boundary between interference and transition. The fit is combined with the use of retaining compound for installation. The process of installation takes longer – it takes 72 hours for the retaining compound to achieve reasonable shear strength but the advantage comes during disassembly. Moderate heat (hair dryer) reduces the shear strength of the retaining compound and facilitates easy disassembly and replacement. There is much less wear on the expensive component which is typically the shaft or the housing. J fits often negate compressive or tensile tolerance stack ups which is an additional advantage.
There are some disadvantages with this methodology. The cure time has already been mentioned. Another key issue which is prevalent in the bike industry is misalignment and ovality. The apertures need to be round and aligned well (bottom brackets). A prime example of the problems associated with this is Trek’s BB90 bottom bracket standard. Trek were one of the early adopters of the shift for sustainability but their BB standard proved to be problematic. Their execution did not place enough emphasis on the need for a reasonably tight hole tolerance. They even went so far as to spec 0.1mm oversized bearings at one point.
It’s noteworthy that in the vast majority of cases, a set of normal bearings at the top end of the size spectrum (as used in the Hambini kit) was sufficient to overcome the problems. In pure engineering terms this is simply a tightening of the standard from J7 to J5.
Another key but often overlooked issue is the perception of the customer. Customers have long expected interference fits between the components so the concept of having what appears to them as a slack fit is associated with poor manufacturing. It will take some time for this engrained idea to be overridden.
Dealing with Bike Manufacturer’s notorious Tolerances
Bike manufacturer’s have long been roasted on the Hambini Barbecue for supplying frames that do not meet their stated tolerances, they have never openly admitted to this and the nearest that any supplier came to an idea of admission is when OPEN cycle famously said “There was no documented standard they were required to meet”, this was in the midst of trying to sue the Hambini YouTube Channel.
Retaining compound and the use of a transition bearing fit does give more wiggle room to deal with undersized bottom bracket holes which are now commonplace in the market. It is not good engineering practice to design for someone else’s inability to manufacture correctly but as a workable solution, it is valid.
Grease attack
There have been reports primarily from the aerospace industry of grease attacking carbon fiber. Strictly speaking the mechanism of attack is to to soften the resin binder material within the composite – it does not attack the carbon itself. Modern carbon fiber composite appears to be fairly immune to this type of attack.
Early carbon frames are still susceptible so it is worth checking.
Of more concern is the frequent specification of poor grade seals in bicycle applications. Cheap bearings, often those found on Amazon and eBay, are fitted with seals that are reportedly nitrile. Genuine Nitrile is resistant to most greases (Shell Gadus, Mobil etc) but there have been reports and pictures of grease attack. In these scenarios it’s almost always due to low grade and misrepresented materials in the bearings.
Grease vs Retaining Compound
Despite the feelings of many armchair bike mechanics, there is no real reason to use grease for static applications. Using grease as an assembly aid is perfectly acceptable but using grease to silence creaking in applications between static components would better be solved with retaining compound. Creaking is movement that emits an audible frequency. The aim is to stop the movement.
Grease is certainly a valuable addition when fits are between metallic materials that are prone to galling – eg aluminum or stainless steel. As an example, using grease between an aluminum bottom bracket and aluminum bike frame would be recommended. However using grease between a metal bottom bracket and a carbon bike frame where all sizes were within permissible range would not be recommended – the grease would reduce the retention force.
Conclusion
The take away from this is the product needs to be correct for the application and that is dependent on what it is being used for and the level of fits between the components. Light fits on static components almost always need retaining compound. Heavy fits between metallic components would be better suited to grease – this is to reduce the chance of galling and installation ease, it is not for performance improvements once installed.
If you are unsure, then the recommendation would be to use retaining compound. It will act as a lubricant for installation (admittedly it is not as good as grease) and “fill” the gaps once it has set.
That’s a relief. I was worried at first because I just installed new SKF bearings in my hubs and I used NGLI 2 grease instead of retaining compound.
*NLGI
The bike shop just put in a new bottom bracket on my old fuji and didn’t use anything and it is ok, so how can you tell if you need anything?
you’d really need to measure the hole first.
What about using temperature shrinkage to fit the bearing (i.e.. putting the bearing in a fridge/freezer) and then letting it expand to the housing. Recommended? Avoid?
Yes you can do that. It’s generally more common to heat the female surface
HAMBINI FOR PRESIDENT
What’s the best way to remove old retaining compound from a carbon bearing seat?
So when would you choose 638 over 641? Is there any downside to the over 2x strength of 638?
Presumably a higher strength would be less likely to allow the bearing to ‘spin’ and damage a frame as you identified in your look Zed video.
As an aside, the commonly used Park RC-1 (which bizarrely Park acknowledge to be relabelled 680) is specified as suitable for up to 0.38mm with a similar 4000 vs 4500psi shear.
Thanks!
acetone will get it off.
acetone might be pretty aggressive to the epoxy used in the “carbon”, it might start softening and expand on the surface!
Acetone doesn’t soften composite by which I mean epoxy with a reinforcement on any 48 hour immersion test we have ever tried in the aerospace industry and I’ve been it 40 years so I cannot see how a grease would do this there’s nothing in it to cause migration
Henkel state in their data sheet for 641, that chemical resistance remains 100% after 100 hours exposure to acetone at 22°.
They recommend Loctite solvent and mechanical abrasion…
What about headset bearings into a fully integrated carbon frame? Would you use nothing or just a small amount of grease?
they should be internally greased, grease on the outside generally attracts dirt.
Re paragraph “Dealing with Bike Manufacturer’s notorious Tolerances”
—
“wiggle room to deal with undersized bottom bracket holes”
should read
“wiggle room to deal with OVERsized bottom bracket holes”
—
or have I missed something?
Could be both!
What’s your hair dressers number? Asking for a friend.
Google Liz Hurley
just did and keep getting images of liz manley instead
Hi Hambini, this was exactly what I asked for a couple of weeks ago (Hard work YouTube channel).
Thanks.
There’s two activators (primers): 7649 and 7471, both hard to source and ridiculously expensive.
Two questions: why do you need to use the activator and which one do you need if you do? The description is nearly identical on Loctite website.
I understand that it speeds up the setting time, and also decreases the product sheer strength which may be helpful for disassembly.
But what if you are happy to wait 100 or 150 hours for it to set? Do you still need it?
I generally use 7649. The datasheet suggests that it cures up the time for curing which is likely accurate. However, practically, I have found the bond generated to be not as strong without the activator. I am unsure of the reason why – I suspect it’s not a mechanical difference but more the retaining compound disperses a bit better when activator is used.
Here you can find technical data sheet of Loctite 638 and graph of cure time for activators, it looks that you don’t need activators if you let it cure for 8 or more hours, keep in mind that is for steel (carbon or alu can be different) and I don’t know does activator help during disassembly
https://docs.rs-online.com/3524/0900766b8130bfaa.pdf
What is recommended to use with threaded connections?
(Axles, stem and seat post bolts etc)? I understand Loctite 243 will be useful for connections which you rarely disassemble, but what about the ones which are taken apart very often?
Further re headset questions: headset bearings in my experience do rust a lot, use of grease is an attempt to prevent that, but what could be the solution?
I can see marks on my integrated carbon headset although I never experienced significant play in them. Could retaining compound be useful there as well? Thanks.
Oh and BTW: Wheels MFG BB voids any warranty if you use a “retaining compound or adhesive”.
Token Ninjas recommendation is to use grease during installation.
I wonder if it is because of their thread together design and that the cups are twisted during installation? Should not be an issue with such a long compound setting time…
Hey Hambini,
You have not published my two last comments. There was nothing offensive there and they were on the subject… I was curious about your opinion. Anyway, another thought: you will not be able to pull that trick with Token Ninja, as its walls are Nylon coated. Activator and 641 may attack Nylon as it is a thermoplastic.
I generally don’t censor anything on here so i would suggest resubmitting if it is not showing up. I have not heard of the activator attacking Nylon but I would check with Henkel to be safe.
Loctite 641 TDS:
http://tds.henkel.com/tds5/Studio/ShowPDF/243%20NEW-EN?pid=641&format=MTR&subformat=REAC&language=EN&plant=WERCS
“This product is not normally recommended for use on plastics
(particularly thermoplastic materials where stress cracking of
the plastic could result). Users are recommended to confirm
compatibility of the product with such substrates.”
It is almost impossible to confirm compatibility… Token states they have not tested compatibility and this do not recommend retaining compounds use.
Other users report that retaining compounds simply do not stick to Nylon or Delrin.
I would go for activator and retaining compound as opposed to retaining compound by itself. Activator is certified to speed up the cure time but anecdotally, lots of people have experienced a much stronger bond with activator and retaining compound as opposed to retaining compound by itself. The reasons for this are probably known to a chemist (might be something tod o with the material being inert) but these kinds of chemicals are used for stuff in regulated industries so they probably can’t put that in the marketing blurb.
Thanks Hambini… As usual, there is no science in cycling maintanance and repairs, no standards. Everything is purely empirical. That’s very frustrating.
But anyway, back to the emperical research. I decided to try installing Token (nylon coated aluminium BB) with just a pure silicone grease. It is a lubricant with very low lubricity. Unlike an aluminium BB, Ninja has a lot more friction with the carbon frame cup. It might not move in the frame at all due to this. If it does, I will try the retaining compound then.
So are you recommending a primer be used prior to the loctite or just use the loctite retention compound on carbon frames. It seems many claim to not use retention compound without primer or otherwise damage to frame can occur. Not clear in the above recommendations.
Primer (activator) must be used whenever the material is inert. Basically, if you are going to use retaining compound. I’d use activator first.
Hi Hambini,
Henkel offers ridiculously big packages (150ml for activator and 50ml for compound).
Another brands offers 10ml bottles which still are more than enough for single application.
Is it suitable to use another brand activator and anaerobic retaining compound which will have comparable shear cut figure ≥6,5N/mm2 as Loctite 641 has?
Of course substitute has the same chemical type: methacrylate ester.
I’ve only ever used Henkel and I wouldn’t use anything else. The other brands might be fine and equivalent but in the applications that I tend to use them on (ie critical ones) I’d rather not take the risk. A bike might be a different story but ultimately it is up to the end user.
Hello Hambini. Your suggestions for carbon frames make sense and I see you do have suggestions for aluminum bb pressed in a aluminum frame. My question is what would the recommendation when pressing a aluminum bottom bracket in to a titanium frame? My worry would be galvanic corrosion. Would this situation require grease? Copper paste? Or a retaining compound? If so which?
Thank you in advance and really enjoyed this technical write up.
Paul
Generally on ALuminium – Ti, The recommendation would be grease.
What’s your view on Wako’s Brake Protector for BB installation? It’s sworn by in Japan for BB installation and creak prevention. Have also known a few Western bike mechanics who ordered big packages from Japan at huge expense – and they usually only want to buy cheap stuff.
I ordered a tube from Japan and am minded to give it a try on the next build.
What are your thoughts on using Park Tool AP-1 and RC-1 for a stainless steel pressfit bottom bracket going into a carbon fiber shell? The concern seems to be with removal. What are the issues with that, if any? Thank you!
I’d recommend Henkel products only because i have used them. I have never tried Park Tools so I can’t comment
What about Loctite 609? What is the best use for it? Cause I see that few manufacturers recommend this as i.e bottom bracket compund
You can use it if you wish. It’s high strength
Hambini, can you comment on a FSA composite (plastic?) PF30 BB pressed into a titanium frame? Retaining compound? Nothing?
You would need to speak to the manufacturer (FSA). As they made it, they would be the best party to get guidance from.
Thanks and sorry about the redundant posting.
“Creaking is movement that omits an audible frequency”. I think you’re trying to say “emit”. Spelling like a dyslexic 5y/o.
I fixed it, thanks for letting me know.
But at least PEN IS Working 😜